Depending on the problem, in the field of fluid dynamics different dimensions have to be considered. There are many phenomena from micro scale (nm/µm) up to macro scale (cm/m) which can have a strong influence on the process. Therefore, in many processes investigations in various scales have to be done.
Research Projects
Wherever heat exchangers are used, the demands on them are becoming ever greater. What is desired is a high heat transfer capacity with the lowest possible pressure loss, combined with a light and compact design.
Therefore, the dimensions of heat exchanger tubes are reduced to channel diameters of less than one millimetre. In this order of magnitude, however, the conventional calculation correlations no longer apply or only apply to a limited extent, since they were developed on the basis of experiments on pipes of larger diameters. Reliable design criteria for such newly developed heat exchanger geometries, both for single-phase and two-phase heat transfer, are therefore still lacking.
The aim of the research project is the experimental and numerical investigation of heat transfer and pressure loss in microchannels. The findings should enable the optimization of heat exchangers with microchannels.
The miniaturization of existing processes in micro-process engineering, the quest for increased efficiency in chemical engineering or the further development of gas sensors are constantly increasing the demands on mathematical models to describe the complex physical processes in microstructures. Ultimately, the goal is to consider all relevant physical and chemical processes in a single simulation tool.
The mathematical-physical description of the growth of a polymer foam will be shown using the example of residual degassing of highly viscous polymers. The aim is to describe the bubble growth and thus the foam volume development as well as the concentration curves of the components and the degassing success.
Often properties of materials that are difficult to access on the size scale to be considered using conventional metrological methods are to be specifically optimized. With the help of numerical simulation, valuable insights can now be gained.
Polyurethane (PU) foams are used in many areas of daily life. The numerical simulations of the production process should reduce the number of necessary experiments on the component and contribute to product improvement.
Many aluminium alloys are considered non-weldable with conventional fusion welding processes. The friction stir welding process can compensate for these disadvantages. The aim of the project is to develop a coupled fluid- and structure-mechanical simulation method for friction stir welding.
The aim of the project is to develop a concept for an energy-efficient system for heating, drying, thawing, keeping warm and baking food.
Kontakt
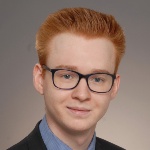
Lars Kirchhof
M. Sc.Scientific Employee
Zishan Mahmood
M.Sc.Scientific Employee